Basic Woodworking Terms for Beginners
As a beginner woodworker, things can get intimidating really fast when you get inundated with terms. I created this list to help you find the definitions of various basic woodworking terms commonly used in the woodworking community and projects.
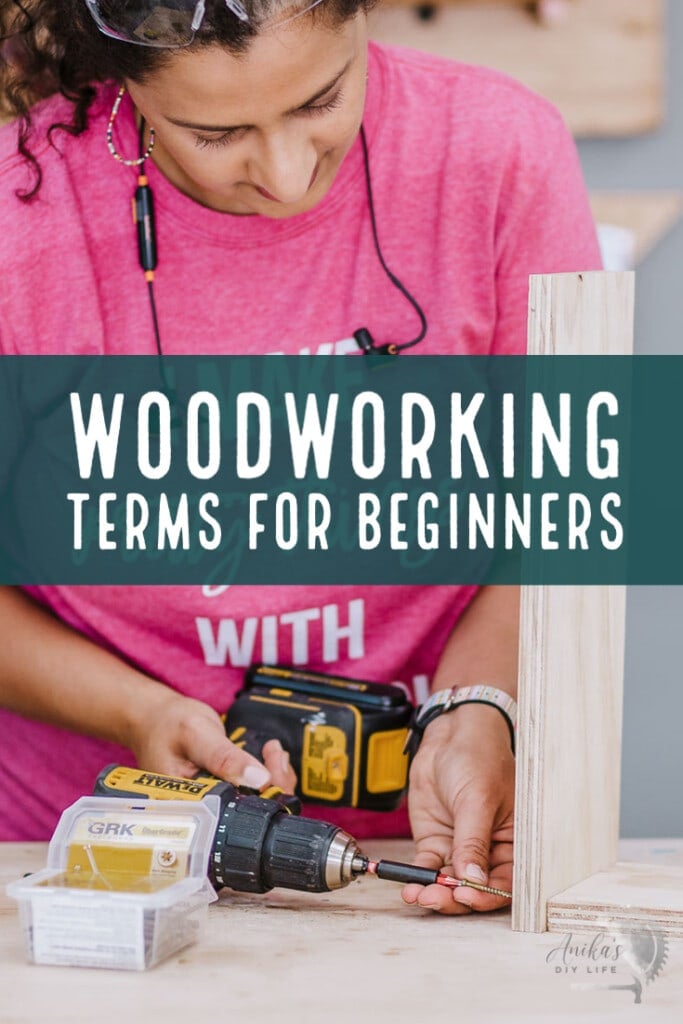
I have tried my best to include as many terms as I could think of but if you find a term that’s not included here, be sure to drop me a note ([email protected])!
Table of Contents
Get a PDF version of this list with definitions in your email for quick reference! Click here.
1. 1X (Also Referred to as “1-By”)
1x or “1-by”, refers to lumber that is 1 inch thick, although the actual thickness of a 1x is ¾” (see actual thickness of wood). This measurement is used for softwoods such as fir, pine, redwood, and cedar and is commonly available in big box stores.
Planing or milling, then drying, causes the lumber to lose about ¼ of an inch. Softwoods are most commonly used by carpenters, cabinet makers furniture makers, and woodcarvers. They are less expensive than hardwoods because the trees grow fast and straight. They can be used to make wall studs, door jams, furniture, etc.
2. 2X (Also Referred to as “2-By”)
2x or “2-by”, refers to lumber that is 2 inches thick, although the actual thickness of a 2x is 1½”. Like a 1x, the milling and drying of the raw material causes the 2x to lose ½” thickness.
2x lumber is also commonly referred to as construction lumber and is used in construction as studs and rafters.
3. 5/4 Lumber
5/4 (referred to as “5 by 4″) lumber is lumber that is 1 ¼” thick. Remember fractions in school? Simplifying the fraction will give you it’s true measurement. Fraction measurements like 5/4 are commonly used for hardwoods.
Hardwoods include ash, birch, cherry, mahogany, maple, oak, poplar, teak, and walnut. They are harder to work with and more expensive to use.
4. Actual Thickness of Wood
Actual thickness of wood is the size of the board once it is milled and dried. Prior to milling the wood is newly cut and green and full of moisture. Once milled, it dries and shrinks to the actual thickness which is the final thickness used in building. When building with it, it is important to design for the actual size of wood.
Before WW1, local sawmills supplied lumber for projects close to their location, so the need for a standard size wasn’t really necessary. Carpenters on the job custom cut the lumber to the size they needed.
As forests were cut back and the demand for lumber increased, the need for shipping wood became necessary and the need for a standard set of measurement arose. That is how we came to have the set standard size of actual thickness of lumber that we have today.
5. Arbor
The blades in your saw need support in the center to connect it to the rest of the saw. A spindle extends out to make an arbor that your saw blade sits on. Saw blades that have an arbor include; miter saw blades, table saw blades, concrete saw blades, abrasive saw blades and panel saw blades.
The hole in the middle of the blade is known as the arbor hole and the blade fits onto the arbor by sliding it through that hole in the saw blade. A precise fit will maintain a steady spin and cut accuracy. It is important to make sure that your blade has the proper arbor hole diameter to fit your saw so make sure to check before you buy a new saw blade.
6. Bar Clamp
A bar clamp is a long steel bar with two clamping jaws that can be adjusted for holding large project pieces and is one of the most commonly used clamps in woodworking. A bar clamp is used for projects that have joinery. It makes it much easier to attach two pieces together when drilling pocket holes or allowing wood glue to set up and dry.
Because of the steel bar, a bar clamp is capable of holding large and heavy workpieces. The bar clamp is almost always used in pairs, but for larger projects it may be necessary to use more than two and you may find you need to cross them over each other to get the hold that you need.
7. Bench Dog
A bench dog is a peg, inserted into a hole on a workbench and used as a stop for a project while it is being worked on. It can be made of wood, steel, or iron.
Holes are spaced 3 to 4 inches apart, and the bench dogs are placed where they are needed to keep the piece from sliding around while being worked on.
Bench Dogs can also be used to elevate a piece from the top of a workbench. Bench dogs can be square or round, but square bench dogs allow for a better gripping surface.
8. Bevel Cut
A bevel is an angled cut made through the thickness of the wood parallel to the face of the board being cut. A bevel cut can be done the entire length of a board or just on the end. It can be cut at any angle except at a 90-degree angle.
A bevel cut can be made using a miter saw, table saw, circular saw or router.
9. Biscuit Joiner
A biscuit joiner a tool that helps join two pieces of wood together. Biscuits are oval-shaped, highly dried, and compressed pieces usually made out of beech or particle wood.
The biscuit joiner cuts a small crescent-shaped hole in each piece of wood to be joined together. The biscuit is then covered in glue and/or the holes are filled with glue, the biscuit is put into the slot of one board and the other board is fitted onto the biscuit on the opposite side.
The boards are then clamped together while the glue dries, ensuring a nice tight bond.
The biscuit itself doesn’t add any structural strength to the joint, they are purely for alignment purposes. It is the wood glue which does the job.
Get a PDF version of this list with definitions in your email for quick reference! Click here.
10. Board Foot
A board foot is a unit of measurement of volume for lumber, 12″ wide by 1″ thick by 1′ long and is used when buying multiple boards in different sizes to calculate the price.
How to measure board foot –
- Measure the length of a rectangular piece of wood in feet and round to the nearest decimal place.
- Measure the width in inches and measure the thickness in inches.
- Multiply all 3 numbers together then divide by 12 to get the board foot measurement.
A board that is 2x2x8 would be calculated 8 x 2 x 2 = 32, then divide by 12 = 2.6667 board feet.
There are online calculators that will do this for you to make it easier.
11. Butt Joint
A butt joint is a type of joint between wooden boards when the end of one piece is placed against another piece and joined.
The two ends meet and do not overlap making a corner. You can make the joint stronger by adding pocket holes, wood screws, finishing nails, dowels, or by adding a triangular piece of wood in the corner.
To make sure you create a good quality butt joint you want to be sure the cuts of the wood are square and as smooth as possible.
12. Caul
A caul is used together with clamps to help apply equal pressure to boards when glued together.
For instance, when making a table top out of plywood, you may glue two pieces together for a thicker top. Just clamps alone won’t ensure that the two pieces of plywood will stay glued together over the entire surface. Adding cauls to the project will apply even pressure over a wider area so that the pieces of plywood will adhere to each other over the entire surface.
Caul’s are typically made from 2x4s and work in pairs. You want to make sure that the edges of the 2x4s meet with no gaping so that when used on a project they will meet and apply pressure evenly.
13. Chamfer
A chamfer is a slope cut in any right-angled piece of lumber. It is used to soften sharp edges and also to prevent damage to them. Cutting a 45 degree angle to remove a 90 degree angle from a project is known as chamfering.
Often it is referred to as a bevel and you will hear or read the terms used interchangeable. However there is a difference in the two. A bevel is just an edge that is sloped, while a chamfer is a beveled edge used to connect two surfaces and normally cut at a 45 degree angle.
14. Chop Saw
A chop saw is a stationary saw that cuts 90 degree angles. Like a miter saw, it has a back fence for holding material in place and it has a circular saw blade with exposed cutting edge. You may mistake it for a miter saw and call it a miter saw, but the two are quite different.
A chop saw is much larger and not able to cut angled, beveled, and compound cuts like a miter saw. The chop saw simply goes straight up and down.
15. Circular Saw
A circular saw’s primary purpose is to make straight cuts in lumber – both cross-cuts in boards and rip-cuts in plywood. It has an encased circular blade and a wide metal base that sits on the material to be cut.
You can set the blade’s depth for the material you are cutting and guide the blade along the line that needs to be cut. Most circular saws allow you to change the base plate’s angle to make bevel cuts too. Circular saws come in different sizes, which is determined by the size of the blade.
Learn more about the pros and cons of the Circular Saw
Get a PDF version of this list with definitions in your email for quick reference! Click here.
16. Clamp
Clamps are used to hold pieces of a project together so they don’t separate while glueing and act as a second, third, and even fourth set of hands for you. They are a must have in the workshop.
They come in a variety of shapes and sizes, but the most popular and useful for woodworking include the C-clamp, bar clamp, spring clamp, edge clamp, corner clamp, parallel clamp, and bench clamp.
The size of clamp you will need depends on the size of your project. The most common size is a 12″ clamp, but clamps can range from 1″ to 50″ in size.
17. Caulk
Caulk is a flexible material used to fill seams to help make them seamless. It is very often used in home improvement, but it can be used in woodworking to fill gaps where wood is joined together in a painted project.
It is also perfect for filling gaps in wall trim. It dries quicker than wood filler. After applying you can easily clean up any excess with damp rag and it’s paintable!
Although it is great for filling seams and gaps, it is not ideal for filling nail holes in wood because it will shrink and cause a divot which will show up in the a painted or stained finish on your project.
18. Countersink
Countersinking is pre-drilling a hole larger than than the size of the head of the screw you will be using so that it will sit flush with the surface and not stick up once it is screwed into your project.
Countersinking is done by using a special drill bit, either a standard or an all-in-one. The standard drill bit results in a cleaner finish, but the all-in-one is easier to line up and can be adjusted to different depths.
When countersinking screws, you can either apply wood filler to hide the screws or drill them deep enough to add dowels to hide the screw heads.
19. Crosscut
A crosscut is a cut that slices across the direction of the grain of your piece of lumber. Think of making boards shorter. When you cut a board to make it shorter you are cutting across the direction of the grain of the wood.
A miter saw is great for pieces that aren’t very wide, a circular saw is good to use if your wood is wider, or you could even use jig saw.
20. Dado
A dado is a groove cut into a piece of wood running across the grain of the wood and is used to connect one piece to another. It is the strongest joint you can make in a woodworking project.
Dados can be cut using a table saw, a router or even a circular saw. The easiest and most common way of cutting a dado is by using a dado blade on your table saw. This is the best saw for the job if the dado will be running the entire length or width of your board. When it doesn’t, you can make your dado using a router and then chipping the cut pieces of wood out using a chisel.
21. Dimensional Lumber
Dimensional lumber is lumber that is cut to standard sizes and is classified only by the depth and width, not the length.
You will know it as 2×4, 2×6, 4×4, etc. It is cut and planed making it immediately ready to use in projects. These are commonly available in home improvement stores.
Dimensional lumber is also the most commonly used lumber for building homes. Dimensional lumber is the same size everywhere, no matter where you go the size of dimensional lumber won’t change. Like all lumber, dimensional lumber has actual (that we have already talked about) and nominal dimensions that we will talk about later.
22. Drill
Commonly called a drill/driver, a drill is a hand tool that is used to drill holes or driver screws. It has a rotating head that holds the drill or driver bit. It can be cordless or corded.
Although the primary function of the drill is to drill holes and drive screws, you can also add attachments to mix paint and concrete, sand surfaces, remove rust.
Various drill/drivers with varying amount of power are available in the market.
23. Edge Banding
Edge banding is a strip of wood veneer with heat sensitive glue on one side which is used to apply to plywood edges of a project for a clean finished look.
Simply cut the edge banding to the length you need it, make sure your iron is set to a least 390 degrees to activate the glue and iron it on. Once it is attached you can go back and trim any overhang on the edges with an edge banding trimmer or just sand it away for a nice smooth finished look. Edge banding can be matched to the plywood species and stained or painted easily.
Get a PDF version of this list with definitions in your email for quick reference! Click here.
24. Edge Joint
Edge joints are used to join boards together edge-to-edge.
The easiest way to do this is using glue then clamping them together until they dry. Biscuit joints can be used to help align boards and cauls to help clamp. They can also be made using pocket holes.
To ensure a smooth seamless joint, the pieces of wood need to be smooth and straight.
25. End Grain
The end grain of wood is the wood that is exposed when it is cut across the growth rings. By cutting a piece of wood at a 90 degree angle instead of the entire length of the trunk of the tree, the end grain is exposed and shows the character of the wood rings and graining.
End grain wood is used when building furniture because of the eye pleasing color and character. The durability of end grain wood makes it ideal for butcher block and flooring. The end grain is prone to moisture absorption, so be sure to seal it.
26. Forstner Bit
A Forstner bit is used to drill a flat bottomed hole. They cut very precise clean edged holes in wood and are guided by their outside edge as opposed to the tip like other drill bits. They leave very little tear out and can be used to drill for cabinetry hardware because you set the depth needed.
Forstner bits have a center spur which helps it cut into wood really well and keeps it from walking off the mark where you want your hole cut and it self clears as it goes. It can also be use to make overlapping holes, holes in the edge of material and angled holes.
27. Kreg Jig
A Kreg Jig is a tool specifically designed to make pocket holes for pocket hole joinery. It is by far the most favorite tool I own and one of the first ones I bought for my workshop.
The Kreg Jig is clamped to one of the boards being joined and holes are drilled through guides to make a precise pocket hole. Boards are attached to each other using pocket hole screws. I promise you will want to put pocket holes in everything once you try it.
You could drill your own pocket holes by hand, but why would you when a pocket hole jig makes it so easy?!
28. Kerf
Kerf is the thickness of the cut that a saw blade makes in a piece of wood and is sometimes used to describe the thickness of the blade itself. It an important thing to know when making furniture, cabinets and other woodworking projects as it determines the accuracy of your cuts.
Kerf width is often disclosed on circular blades used in table saws and miter saws, but not on bandsaw blades that are very thin.
29. Miter Cut
A miter cut is an angled cut across the width of the board. This is made by moving the table to the required angle. For example, 45° is a very common angle, but any angle other than 90 is considered a miter cut.
The two 45 degree angles will meet in a project to form a 90 degree angle or corner like you have on a picture frame. You will notice that miter cuts are cut on the face of the wood and when two are joined together they make a miter joint that we will talk about next.
30. Miter Joint
A miter joint is a made by cutting each part at a 45 degree angle so that when they meet they for a 90 degree angle or corner. Miter joints are used in door and window making, cabinets and boxes, picture frames and all types of moldings.
A miter joint only shows a seam where it is joined and can be concealed easily with caulk or wood putty for a smooth finish. Miter joints are weak, so they should not be taking any weight without also being reinforced with another joining method.
Get a PDF version of this list with definitions in your email for quick reference! Click here.
31. Miter Saw
A miter saw is a saw that can cut across a board at any angle. Every miter saw is made up of the following parts; blade and guard, fence, miter gauge, bevel gauge, and handle and trigger. The blade is a circular blade that is encased half way and turns in a circular motion when you pull the trigger.
There are also different types of miter saws; basic miter saw, single bevel compound miter saw, double bevel compound miter saw, and sliding compound miter saw. Miter saws are designed to make crosscuts, beveled cuts, miter cuts, and compound cuts.
32. Nominal Thickness of Wood
The nominal thickness of wood is the standardized size “name” given to a measurement of a piece of wood. It is not the actual size of the cut of wood. Nominal thickness is the name of the lumber not the size.
For instance, 2X4 is a common name for a piece of lumber and we have all heard that name, but the size of an actual 2×4 is not 2 inches by 4 inches. The reason for the difference in nominal and actual is the dressed size after a piece of wood has dried and been planed. See actual thickness of wood.
33. Plywood
Plywood is a manufactured wood product, made from plies of wood veneer that are glued together. There are many different types of plywood and different grades. The higher the grade, the better the quality and the higher the price.
Plywood is strong and durable and is an excellent choice for furniture projects. It can be significantly cheaper than fine lumber – especially when dealing with large wide boards. It can be used to make any furniture project like dressers, wardrobes, built-ins, media consoles, shelves, and many many others. Like any type of wood you purchase there are nominal and actual sizes of plywood.
Standard or nominal sizes of plywood range from 1/8″ to 1 1/4″. A standard sheet of plywood comes in 4′ X 8′ sheets which is the common size for spacing on floor joists, roof trusses and wall studs.
RELATED: DIY Plywood Headboard
34. Pocket Holes
A pocket hole is an angled hole that is drilled into one board. When you screw in through the angled hole to attach two boards, an extremely strong joint is made.
Benefits of pocket holes include extremely beginner friendly way to do joinery in your projects, the joint is super strong, there is no clamping needed when waiting for glue to dry and it makes alignment of two boards straightforward.
You can make your pocket holes by hand or you can use a pocket hole jig like the Kreg Jig.
Get a PDF version of this list with definitions in your email for quick reference! Click here.
35. Predrill
You should pre-drill pilot holes in wood to prevent splitting and cracking of the wood around the screw hole. Driving a screw into wood displaces the wood that is there, making room for the screw. The displaced wood puts more pressure on the wood around the screw which can cause it to spit and crack.
There is nothing worse than to be working on a project only to have discard a piece of wood because it has split. To keep this from happening, simply use a drill bit that is the same size as the body of the screw not including the threads and pre-drill for the screw.
36. Rip Cut
A rip cut divides a piece of wood parallel to the grain for a lengthwise cut, unlike the crosscut above that cuts across the grain. It is used to cut large sheets or timber or boards down to size.
The best saw to use to do rip cuts is a table saw because of the built in fence, but if you don’t have a table saw you can do it with a circular saw or jig saw, just be sure to use a straight edge to keep your cuts nice and straight.
37. Router
A router used in woodworking can cut patterns, grooves, and designs in wood. It can be fix based or a plunge type and can be handheld or stationary. You can use a router to trace the design you want and then re create that design in multiple pieces of wood.
Routers can be used for making perfect edges, shaping molding, cutting easy dadoes, carving out clean rabbets, creating patterns and much more. The type of router you use is dependent on the type of project you are doing.
38. Speed Square
A Speed Square is a triangular carpenter’s tool. It is also commonly known as a rafter square or a carpenter’s square. The term “Speed Square” is trademarked by Swanson Tool Co., Inc. but is commonly used as a generic name.
The main purpose of the Speed Square is to layout lines very quickly and accurately. However, you can also find and draw angles and circles, adjust or guide a saw, and even use it as a level!
A Speed Square is packed with features that make for uses well beyond the most obvious one – using it as a way to square boards.
RELATED: How to Use a Speed Square for Beginners
39. Table Saw
A table saw is a type is saw used to cut material. The blade is mounted in the center of a “table” and spins as you feed material across it to cut. It can open up possibilities of the kind of cuts you can make – rip, cross-cut, miter cut, square, dado, and rabbet.
A table saw features a blade that you can raise and lower depending on the material you are cutting, has a fence parallel to the cutting blade, and it can cut plywood, hardwood plastic laminate, and melamine.
A table saw can help you do a vast variety of things if you have the right jig. It opens up a whole world of possibilities for various advanced joinery techniques too!
40. Tape Measure
A tape measure is a flexible ruler made with fiberglass or metal and is expandable and retractable inside the case. It has a thumb lock to keep it in it’s extended state while measuring.
Tape measures come in imperial (inches and feet) and metric (centimeters and meters) units of measurement.
A tape measure has plenty of hidden features to make life easier and make reading them more accurate and I list them all in How To Read A Tape Measure And Other Clever Features.
41. Veneer
Veneer is a thin layer of hardwood that is usually thinner than a 1/8 of inch and is bonded or glued to a cheaper surface underneath it. A lot of times it will be adhered to plywood or particle board.
The use of veneer allows furniture makers to make beautiful looking pieces of furniture at a lower price. Remember the edge banding we talked about earlier? That is an example of veneer.
Although we think we wouldn’t want furniture made using veneer, it is actually more sustainable because it uses less wood than the same piece of furniture made with solid wood.
42. Workpiece
A workpiece is the piece of wood you are making into the project you are building. You will cut it, join it, sand it, drill it, stain or paint it until it becomes the finished product you were hoping for.
The term “workpiece” was established with the crafts and manufacturing industry to provide a relationship between the work done and the piece the work is being done on.
Get a PDF version of this list with definitions in your email for quick reference! Click here.
See lots more beginner woodworking articles here.
Anika's goal is to inspire and empower beginners with woodworking, DIY, home improvement, and home decor ideas.
She wants everyone to unlock their creative potential and experience the feeling that comes with making something. Nothing feels better better than seeing something and saying "I can make that!"
Great start! Some other common ones, rabbit and impact driver are terms a beginner would come across. Perhaps clamps and their various forms c-clamp, f-clamps, parallel clamps, pipe clamps, corner clamps, bar clamps, etc. Great job with the lumber terms, so many people, get confused with linear vs board feet and other ways lumber is measured that’s just not intuitive to a beginner.
Thanks! Adding to the list for the next update in a few weeks.
Very well Explained! Great work!